Working principle of PCB Depanelizers
The working principles of different types of
PCB depanelizers are also different. The working principles of PCB depanelizers are mainly designed according to different PCB boards. The products made by each customer are different, and the types of PCB boards are also different. Therefore, different PCB cutters should be used for different PCB boards. Different PCB depanelizers have different working principles, and share the advantages and disadvantages of different types of PCB depanelizers.
1. For small, thin and relatively simple PCB boards, use the
guillotine PCB cutting machine to cut.
The guillotine PCB cutter machine adopts the latest pneumatic electric lightweight design to complete the plate cutting stroke without shear stress at one time, especially suitable for cutting precision SMD or thin plate; The bow and micro cracks generated when there is no circular knife type plate cutting. The wedge-shaped tool is used for linear plate cutting to minimize the shear stress, so that the sensitive SMD components and even capacitors can not be affected, and the potential quality risk of the product can be minimized.
2. For PCB boards with components, when the components are not very high, use the blade moving type PCB separators.
The utility of the knife type PCB separator machine is very strong. After soldering, the breaking of multiple boards will often damage the circuit or break the electronic parts. Moving and splitting with the knife type PCB cutting machine can completely reduce the stress, prevent the cracking of solder joints and parts, and improve the production efficiency and quality; The upper round knife and the lower flat knife are adopted. When the board is on the lower flat knife, the switch is stepped on, and the upper round knife moves laterally to the set point, that is, the PCB board is cut and divided without wire falling off, and the incision is flat without burrs. A conveying platform can also be installed to facilitate the automatic delivery of cut PCB boards.
3. Special shaped and irregular PCB board, stamp hole board, multi-point board, using
milling cutter PCB router machine.
The milling cutter type PCB router machine mainly uses the equipment that the milling cutter operates at high speed to separate the multi connected PCB according to the pre programmed path, instead of the cutting defects of manual breaking or V-CUT or push. It has high and accurate cutting precision, long service life, good cutting quality, no dust, no burr, low stress, safety and simplicity, improves the product quality and reduces the scrap rate. It is mainly used to segment special-shaped and irregular PCB board, stamp orifice board and multi-point board. The cutting stress is smaller, so as to prevent chips such as PCBA board capacitor from being damaged in the cutting process; Avoid tin crack and component damage caused by manual folding.
In the market, the PCB board requirements of various products are different, so there are PCB separator machines with different working principles to cut different PCB boards. Different types of PCB separators have different working principles, such as dust treatment, as follows
Dust treatment of working principle of PCB separators:
Due to the single working principle of guillotine PCB separator and knife walking PCB separator when cutting PCB boards, industrial dust collection equipment cannot be configured. Therefore, in the process of cutting, the dust on the desktop accumulates to a certain amount and needs to be cleaned manually. Disadvantages: in the process of cutting, dust is everywhere. The dust range cannot be controlled and can only be cleaned manually. There is also dust on the PCB board, which needs to be cleaned manually.
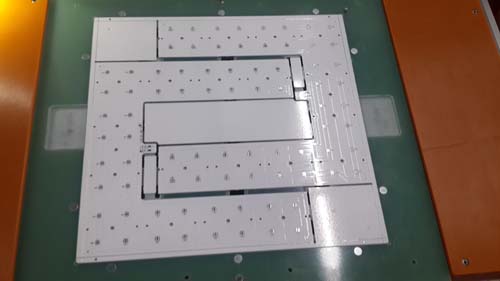
The dust generated in cutting PCB board needs professional industrial dust collection equipment to solve.
For example, the gam series milling cutter router machine is equipped with industrial dust collection equipment - dust collector, plus electrostatic eliminator. The dust cleaning methods can be selected from the upper and lower methods, which completely absorbs the dust generated by the automatic PCB cutting machine, without manual cleaning of the dust generated in the cutting process, and the PCB board will not be stained with dust, There is no need to wash PCB. While saving labor, it greatly increases the production efficiency.